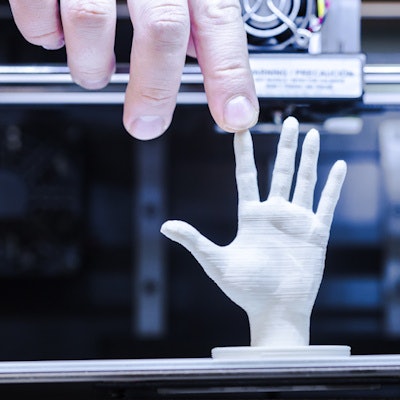
As specialists in the viewing, manipulation, and interpretation of 3D medical datasets, radiologists are in the ideal position to exploit the full potential of 3D printing, but their lack of knowledge of the process endangers moving them forward, according to researchers from a top London hospital.
Three-dimensional printing has applications in orthopedic, cardiovascular, otorhinolaryngological, abdominal, and oncological specialties, and the software tools available for the creation of 3D models are now widely available and straightforward to use, noted Dr. Jeremy Lynch, a neurointerventional fellow at King's College Hospital NHS Foundation Trust. It enables radiologists to add value by making imaging findings tangible and understandable for patients and physicians, and facilitates a personalized approach to aid communication of imaging findings. Also, it has great potential for training, preoperative planning, and in medicolegal cases.
"There's a growing interest in 3D printing," he said in an online presentation on the European Society of Radiology (ESR) website. "3D printing is a technology that should be owned by radiologists. It can be done with minimal skill and very cheaply."
It's now feasible to convert a DICOM file to 3D model using completely free software at a total cost of around 20 pounds (23 euros), added Lynch, who conducted the work on 3D printing while he was a radiologist at the Chelsea and Westminster Hospital, also in London.
The technology explained
Three-dimensional printing is the synthesis of real objects from digital models. It was first described in 1983, and craniofacial and maxillofacial surgeons were among the early adopters. It is used primarily in reconstructive procedures for the creation of custom-made implants, prostheses, and guides. For example, metallic plates can be directly tested on 3D-printed skulls or designed on a computer to match the patient's specific anatomy and printed out.
The advent of more affordable consumer-grade printers has led to a rapid growth in applications of the technique over recent years, but DICOM images cannot be directly printed, Lynch explained. The required structures must be separated from the raw data and converted into a file format the 3D printer can understand.
Cerebral vasculature can be printed to a high resolution and can be used to plan interventional and surgical procedures such as embolization, coiling, and clipping, while 3D-printed models can assist in complex spinal surgery cases, but it has been challenging to accurately print the internal lumen of vasculature because the walls may be very thin and not visualized on imaging due to the use of contrast, he continued. Printing out cardiac models with complex congenital abnormalities prior to surgery has been shown to improve spatial orientation, offer better understanding of complex pathologic conditions, and increase surgeon satisfaction.
"An area where there is great scope for future development is simulation training," Lynch said. "A role for 3D printing has also been suggested for medicolegal purposes. A 3D model of a brain from a child with hypoxic ischemic encephalopathy was shown to demonstrate the substantial physical differences compared with a normal brain, which could be used in court to show the extent of disease."
Step-by-step guide
A volumetric sequence dataset (CT or MRI) retrieved from a PACS archive is necessary to create a model. The resolution of the finished product will depend on the initial study resolution; 1 mm slices are sufficient for solid organs, but fine vasculature and intricate bone detail will require a higher resolution, he said. Modern 3D printers can print in excess of the resolution of most volumetric radiological studies.
At Chelsea and Westminster, they use a free software package, Horos, to view, process, and export data. This DICOM viewing and manipulation tool is derived from OsiriX, and these packages offer 2D and 3D rendering tools, including multiplanar reconstruction (MPR), surface rendering, volume rendering, and maximum intensity projection (MIP).
There are many ways to achieve segmentation, but the most common is to select structures by similar attenuation value (CT) or signal (MRI). Structures that are well delineated and have greater contrast relative to their adjacent structures will segment more precisely, Lynch said. Bony structures on CT have high attenuation values relative to soft tissue and segment very well. For the same reason, contrast administration is helpful for segmentation.
"In OsiriX it is possible to select 3D regions of interest by picking a voxel and setting upper/lower bounds for attenuation values according to the values present in the anatomical structure. OsiriX then grows this region using a mathematical algorithm," he noted.
The technique has limitations. Often the contrast between structures is not great enough for the algorithm to separate them. A segmentation tool, Mia-Lite (Medical Image Analysis Solutions), using a more intelligent algorithm can be installed into OsiriX. It is essential to specify upper and lower threshold attenuation values for CT so values outside of this range do not appear in the region of interest, and blocking regions also can be defined manually. One or more growing regions must then be chosen within the tissue of choice, and from these regions, the program will compute and identify all the neighboring pixels between the growing regions within the threshold range as determined by the algorithm.
Once a new series has been created, it can be transformed into a 3D surface-rendered model, Lynch continued. STL (STereoLithography) is the most common format, and describes solely the surface geometry of 3D objects. Other file formats include OBJ and VRML, which can allow representation of color, texture, and other attributes.
The STL file generated by Horos often requires modification to make it suitable for printing. There may be residual artifacts or errors generated by segmentation or unnecessary detail, e.g., on the inside of an object. Software allows the object to be viewed as a 3D mesh, the polygonal faces and edges of which can be edited and manipulated. For instance, MeshMixer is powerful and has an intuitive user interface, while Blender offers greater functionality, but manipulation of the object and navigation through the software are more challenging.
Use of editing tools
Editing tools can cut out unwanted features by hand, reduce or enhance protruding edges, and surface render the object for visualization prior to printing, he said. Holes in the mesh can be filled or bridged. Nonmanifold edges (edges that are not connected to another face) must be eliminated because they are not printable.
The resolution of 3D printers can be greater than that of the DICOM data, so models can look pixelated, but tools can automatically smooth the structures' surfaces to produce a better result. The detail of the object depends on the number of triangular faces it is composed of, but structures generated by STL export may have extraneous triangles that do not contribute to the resolution, and polygon reduction can enable the size of the file to be reduced without a significant difference in quality/resolution of the final model.
"It is sometimes necessary to fill holes to aid the printing process. These may be pre-existing unwanted holes or holes created in postprocessing by cutting out superfluous components/artefacts," Lynch said. "Three-dimensional printing software is also able to prepare the design for printing in terms of shell thickness, support structures, infill patterns and printing axes/orientation."
The object should be orientated for printing so that the wider and flatter parts of the object are positioned at the base (first printing layers) and the finer more intricate structures within the top layers. This will allow it to be more stable and necessitate fewer supports.
Slice thickness, material, and speed of printing (extrusion rate) can be adjusted. Decreasing slice thickness allows a more detailed model but increases the time of printing. Most printers can print within a resolution range of between 0.3 mm and 0.01 mm, but some ultrahigh-resolution printers can print layers as thin as 0.001 mm. The speed of the printer head can be increased, but at a threshold (usually around 150 mm/sec to 200 mm/sec for extrusion printing) accuracy decreases and the printer can overheat. Some printers can print two or more materials/colours simultaneously using multiple extruders.
Cost comparisons
The Chelsea researchers submit tbe processed STL file to an independent company via the 3DHubs website. This enables them to compare the prices of many local printers. They prefer to print out their model at half-life size dimensions, thereby reducing cost and time to print. Often they choose a printer called Witbox 2, which uses material extrusion (fused deposition modeling), and white polylactide (PLA), a biodegradable and bioactive thermoplastic aliphatic polyester derived from renewable resources. The layer height can be 0.2 mm, which is sufficient for maximum resolution, and the print time is 14 hours using an extrusion rate of 80 mm/sec.
Lynch's colleagues involved in this project are Dr. F. Sheikh and Dr. E. Guilhem, who are both specialist registrars in radiology at Chelsea and Westminster. The group shared its experiences in an e-poster at ECR 2017 that's available on the ESR's EPOS database by clicking here.